Turning heatsink process
turning technology allows for high aspect ratios and high fin densities, further increasing the heat dissipation surface area and thermal conductivity efficiency of the heat sink. Through optimized design and manufacturing processes, the contact area between the fins and the base is optimized, enabling skived heat sinks to achieve optimal thermal conductivity through manufacturing, aiding in more effective heat transfer to the surface of the heat sink. Skived heat sinks can provide excellent heat dissipation performance in confined spaces, making them the preferred heat dissipation solution in limited space conditions. For certain high-heat applications, turning technology is one of the most cost-effective and reliable methods for producing heat sinks. The manufacturing process is subjected to precise control, ensuring product quality and stability, while also reducing manufacturing
Advantages of turning heat sinks include:
-
High-Efficiency Heat Dissipation: Due to the use of highly conductive materials, Skived Heat Sinks effectively conduct heat away from the heat source.The skiving design increases the surface area of the heat sink, further improving the efficiency of heat dissipation.
-
Selection of High-Quality Materials: With turning technology, various high-performance materials such as aluminum alloys, copper, and copper alloys can be utilized for heat sink manufacturing. These materials possess good thermal conductivity and corrosion resistance, ensuring the stable operation of the heat sink over time.
-
Precision Machining: Turning technology provides highly accurate machining capabilities to precisely shape and size heat sinks according to design requirements. This ensures proper fitment of the heat sink with other components, enhancing the overall system performance and reliability.
-
Customized Design: Turning technology allows for the customization of heat sink design and manufacturing according to specific customer requirements. Whether it's size, shape, or surface treatment, adjustments can be made to meet the demands of various application scenarios.
-
Cost-Effectiveness: Compared to other manufacturing methods such as casting or extrusion, turning technology typically offers lower costs. Since turning technology can complete multiple machining steps in a single operation, it can reduce manufacturing time and costs.
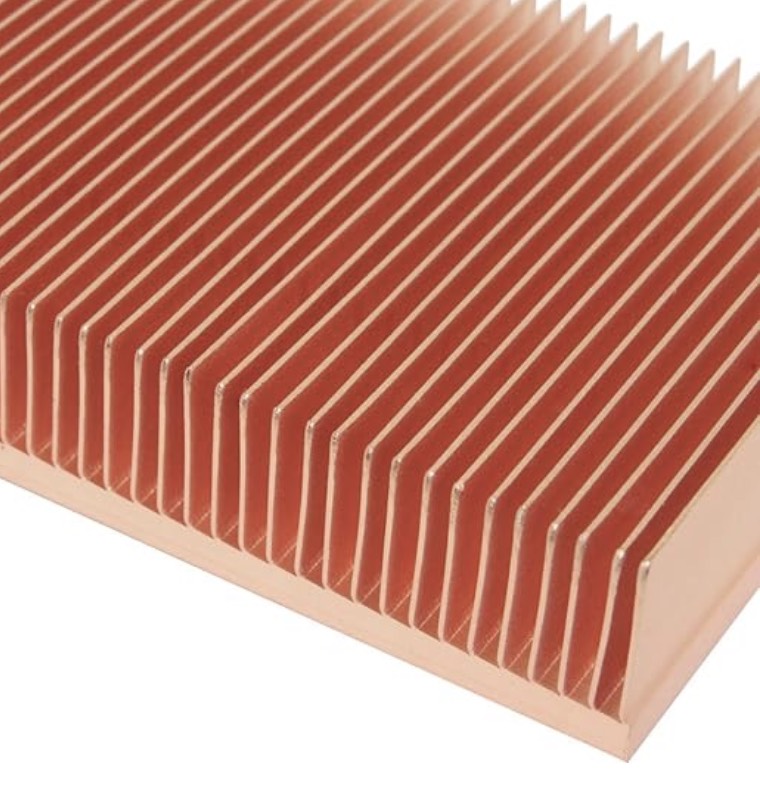
-
Nickel Plating 10um Skived Heatsink
The Nickel Plating 10um Skived Heatsink offers exceptional heat dissipation through its precisely designed skived fins, providing a larger surface area for optimal cooling. The 10-micron nickel plating ensures corrosion resistance and enhances thermal performance, making it ideal for high-power applications. Suitable for electronics, telecom, and industrial equipment, this heatsink effectively dissipates heat to maintain component longevity and reliability, ensuring superior system performance. The skiving process creates durable fins that enhance thermal efficiency while the nickel coating offers robust protection. -
Copper Heatsink Skived
The Copper Skived Heatsink is designed to provide superior thermal conductivity for high-power electronic applications. Manufactured from high-purity copper, it utilizes skiving technology to create efficient, high-density fins that maximize surface area for improved heat dissipation. This heatsink is ideal for applications where effective cooling is critical to prevent overheating and ensure the longevity of electronic components, such as in power electronics, LED lighting, and data servers. The skived copper structure ensures uniform heat distribution and high cooling efficiency, making it suitable for high-performance thermal management. -
Power Supply Heatsink Skived
The Power Supply Skived Heatsink is engineered for high-efficiency thermal management in power supply units. Crafted using precision skiving technology, it features closely packed aluminum fins that maximize surface area for effective heat dissipation. This heatsink is ideal for cooling high-power density components, reducing the risk of overheating, and extending the lifespan of sensitive electronics. Its robust design ensures consistent performance in demanding environments, making it suitable for industrial power supplies, converters, and inverters. The skived construction guarantees optimal thermal conductivity, ensuring reliable cooling in critical power applications. -
Heatsink Skived FPGA
The Skived FPGA Heatsink is specifically designed for field-programmable gate array (FPGA) cooling solutions, using advanced skiving technology to enhance heat dissipation efficiency. Its multiple fin structure offers increased surface area, maximizing airflow and thermal performance. Constructed from high-quality aluminum, it ensures efficient heat transfer while maintaining a lightweight design. Ideal for FPGA applications in high-performance computing, telecommunications, and industrial automation, this heatsink is built to prevent overheating and maintain optimal operating temperatures, ensuring reliable FPGA performance under demanding workloads. The skived design delivers consistent, effective cooling for critical electronic components. -
Fluid Cooled Skived Heatsink
The Fluid Cooled Skived Heatsink is designed for efficient heat dissipation in high-performance applications, combining a skived fin structure with fluid cooling channels to enhance thermal management. Ideal for use in electronic devices that demand effective cooling, this heatsink features a precisely engineered skiving process to create uniform and high-density fins, optimizing surface area for improved heat transfer. The integrated fluid cooling further enhances its cooling capabilities, making it perfect for environments requiring superior thermal control, such as data centers, power electronics, and advanced computing systems. -
Cu1100 Skived Heatsink
The Cu1100 Skived Heatsink is constructed from high-quality copper (Cu1100) to ensure superior thermal conductivity and optimal heat dissipation. This skived fin heatsink features tightly spaced fins formed from a single copper block, maximizing surface area for effective cooling. Its excellent thermal properties make it ideal for high-power electronic components, providing reliable heat management for demanding applications, such as power electronics, telecommunications, and industrial automation systems. The skiving process results in enhanced mechanical strength and consistent performance, ensuring a highly efficient thermal solution for various high-performance environments.
1. How do Skived Heat Sinks work?
Skived Heat Sinks operate by cutting a metal material (usually aluminum or copper) into multiple thin and flat strips, then stacking these strips together. This structure increases the surface area of the heat sink, thereby enhancing the thermal conductivity efficiency. When electronic devices generate heat, this heat is conducted to the surface of the heat sink through thermal conduction, and then dissipated into the surrounding environment through convection and radiation.
2. What applications are Skived Heat Sinks suitable for?
Skived Heat Sinks are widely used in various electronic devices, including but not limited to power adapters, LED lighting, automotive electronics, communication equipment, computers, and industrial control systems. They are especially suitable for situations where space is limited or where there are high demands for thermal management.
3. How to choose the right Skived Heat Sink?
Choosing the right Skived Heat Sink involves considering the following factors:
-
Thermal Load: The amount of heat generated by the device is a key factor in selecting a heat sink.
-
Space Constraints: The size and shape of the heat sink need to fit within the spatial layout of the device.
-
Environmental Conditions: The temperature and humidity of the working environment can affect the cooling performance.
-
Cost: Budget is also a factor to consider when selecting a heat sink.
4. What should be noted about the installation and maintenance of Skived Heat Sinks?
-
Proper Installation: Ensure good contact between the heat sink and the heat source; sometimes thermal paste is required to improve thermal conduction efficiency.
-
Regular Cleaning: Regularly remove dust and debris from the heat sink to maintain good heat dissipation performance.
-
Avoid Physical Damage: Handle with care during installation and cleaning to avoid bending or damaging the skived strips.
5. Will the performance of Skived Heat Sinks decrease over time?
Under normal operating conditions, the performance of Skived Heat Sinks does not significantly decrease over time. However, if the heat sink is covered with dust or debris, or if its physical structure is damaged, its cooling efficiency may be reduced. Therefore, regular cleaning and inspection are key to maintaining its optimal performance.
Leave a message!
Our professional team will reach you within 24hrs!
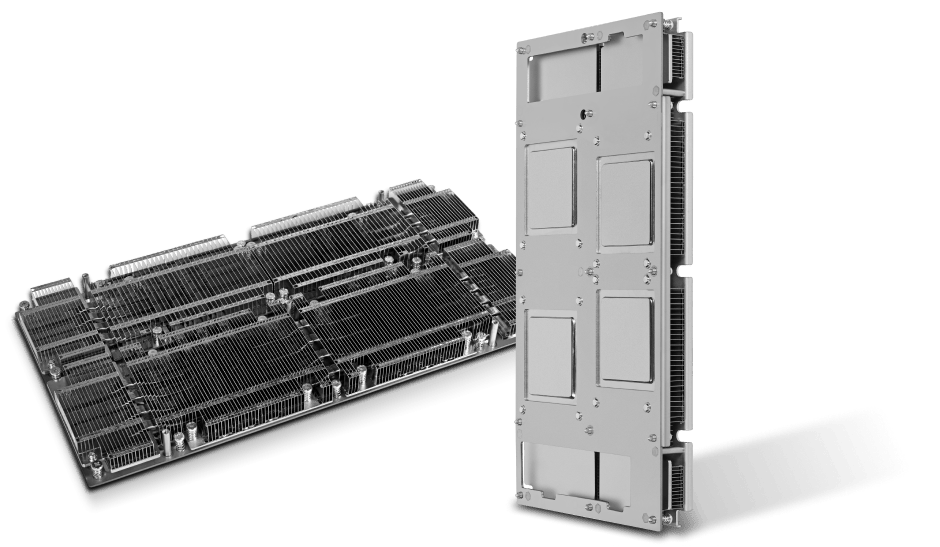
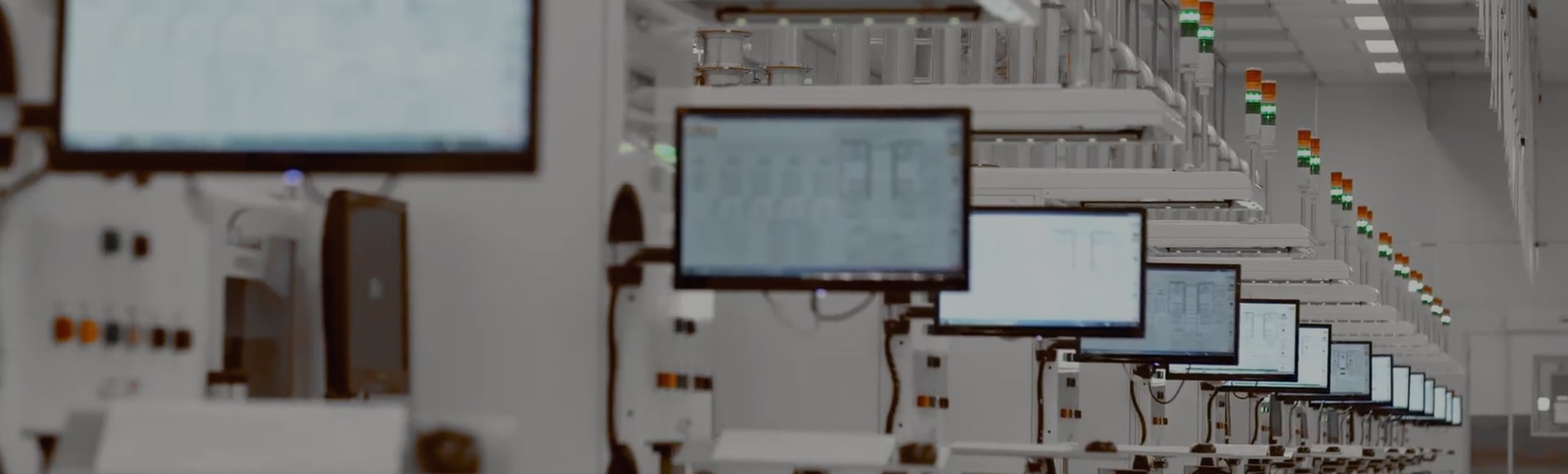